Digital Milk factory
Digital Milk Factory is an ambitious innovative project whose main aims are:
- Visualization of all factory processes.
- Optimization of processes and avoidance of any time-based weaknesses in the production.
To implement the ambitious “Digital Milk Factory” project our team needed to develop a truly universal system based on our cloud service in combination with reliable and cost effective sensors. Our capable team was able to create a comprehensive solution, which satisfied every project specification.
The cloud solution was introduced into all production stages from diesel generator monitoring to temperature control and is ready to offer even more.
Primarily, the platform ensures control over diesel generators on-site. Apart from the established online fuel consumption control, operators are getting live information on generator status (standby, switching mode (UPS-GRID)) and grid status. Moreover, special controllers sending data to cloud allow to control power supply to production equipment. If anything goes wrong event-based notification system guarantees prompt reaction to any alterations, thus preventing critical equipment breakdowns.
Satellite monitoring system is also used to control water supply system including water tanks and water pumps. The solution makes possible uninterrupted operation of the pump throughout the factory working time, eliminating outages and work stoppage. By analogy with fuel level control, additional hardware combined with notification system allows to control water level in the tanks. Upon reaching minimum or maximum accepted levels the corresponding notification is triggered signifying the need for interference.
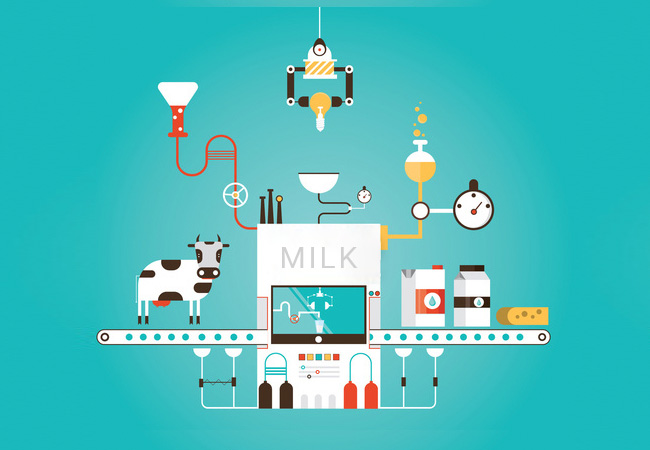
Last but not least, the temperature control system is used to maintain the corresponding thermal environment in the rooms for yogurt processing. A responsible person gets an alarm notification whenever the temperature exceeds specification limits and takes action to prevent the spoilage of tons of dairy products.
As a result the client acquires visualization of all factory processes in the Sensolator and further analysis allows for overall production optimization and better figures of the time-based variables.
The project is still underway and operating procedures are constantly being supplemented by new “smart” methods. The factory is now few steps away from using satellite monitoring system to control hot and ice water installations, cooling systems and the whole treatment plant of the factory.
Main Monitoring parameters:
- Diesel Generator – control of generator status (stand-by, switching mode (UPS-GRID)), Grid status, Fuel monitoring;
- 100 m3 water tank – water level with pre-setup two alarm levels – 10% and 20% of water level is reached – sound and light alarm;
- Water pump – control of working status of water pump, providing water to 100m3 water tank, sound and light alarm is generated if pump is not working more than 30 minutes in factory working time;
- Temperature control of two hot rooms for yogurt processing – sound and light alarm is generated if temperature is above preset values;
- Control and monitoring of power supply of equipment (controllers providing information to control room);
Next stages are:
- Connecting for monitoring and control of the hot water installation;
- Connecting for monitoring and control of the ice water (0 – 4°C) installation;
- Connecting for monitoring and control of cooling systems;
- Connecting for monitoring and control of treatment plant of the factory.